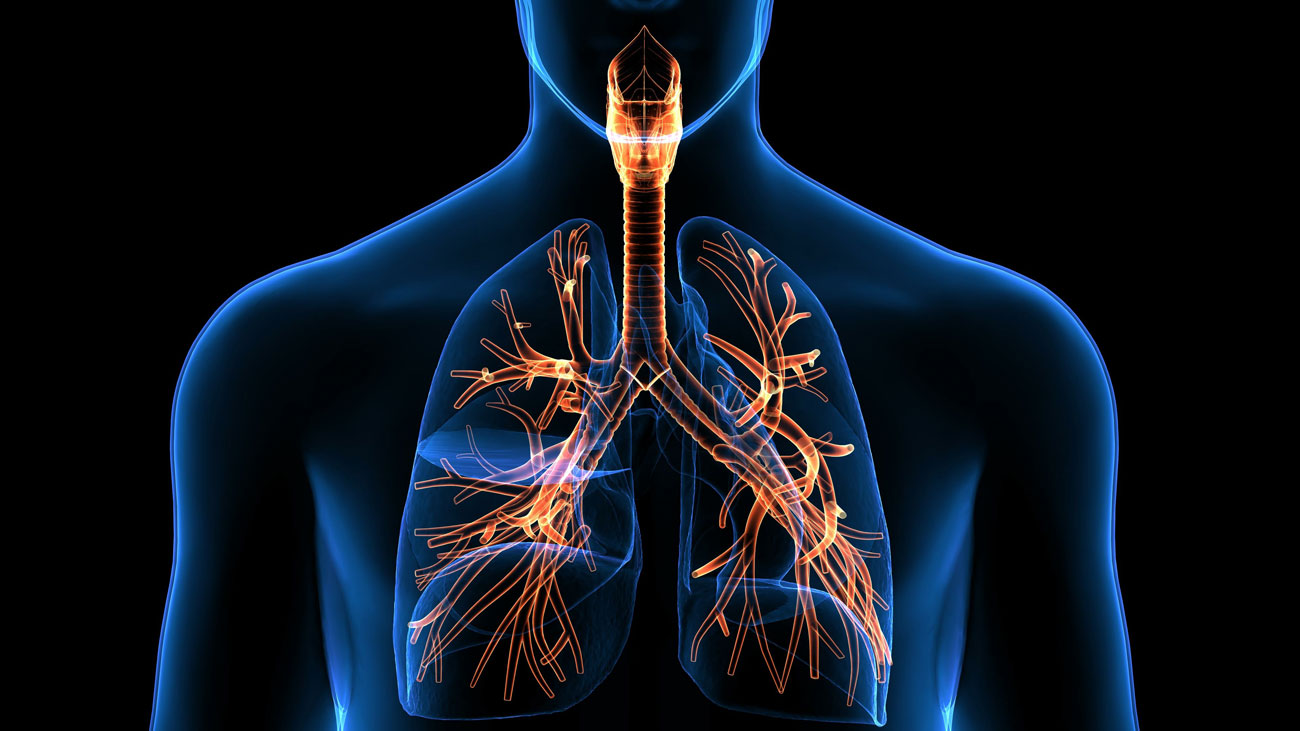
Respiratory diseases: current developments
The annual statistics on work-related ill health and workplace injuries for 2022/23 show 12,000 people die each year from lung diseases linked to exposure to hazardous substances at work. In addition, 19,000 new cases of breathing and lung problems are thought to have been caused or made worse by work.
Breathing in certain dusts, gases, fumes and vapours in the workplace can cause serious long-term lung damage. Diseases like asbestosis, silicosis, chronic obstructive pulmonary disease (COPD), asthma, emphysema and even lung cancer all cause severe, often incurable health problems that can ruin lives.
Occupational lung diseases typically have a long latency (they take a long time to develop following exposure to the agent that caused them). Therefore, current deaths reflect the effect of past working conditions.
What we’re breathing in became a very real concern in 2020 as we donned masks to prevent the transmission of Coronavirus. However, recent cases and campaigns reveal there are other air pollutants that too many workers are still being exposed to. Let’s take a look.
Dust
Dust is a silent and sometimes invisible killer, says the HSE. Dust particles can be 100 times smaller than a grain of sand. You don’t need to see them to breathe them in. Once in your lungs, dust will start causing damage.
Thousands of cases of irreversible lung diseases, such as silicosis, are reported annually. Caused by exposure to dust at work, such diseases are preventable, but tragically can be life-changing or even result in loss of life.
There are three main types:
- Silica dust – created when working on silica-containing materials like concrete, mortar and sandstone (also known as respirable crystalline silica or RCS).
- Wood dust – created when working on softwood, hardwood and wood-based products like MDF and plywood.
- Other ‘general’ dust – created when working on other materials containing very little or no silica. The most common include gypsum (e.g. in plasterboard), limestone, marble and dolomite.
In the summer, the HSE undertook a series of investigations focusing on respiratory risks from exposure to dust. The inspections, part of a respiratory health intervention initiative, focused on dust control, checking employers and workers know the risks, plan their work and are using the right controls.
HSE’s chief inspector of construction, Michael Thomas, said:
“Every year we see construction workers die from diseases caused or made worse by their work. This is unacceptable in the 21st century, when occupational lung disease is preventable. We are urging employers and workers to take the necessary precautions today to protect their long-term lung health, to avoid them and their families suffering from the devastating impact that can result.”
The initiative was supported by HSE’s Dust Kills campaign. This provides simplified advice and guidance on the Work Right website, for employers, small builders and workers, to help everyone understand the risks and how to stay healthy on site.
In October, a Northwich furniture company was fined after it repeatedly failed to protect its employees from exposure to wood dust. Pineland Furniture Ltd was inspected by the HSE on two separate occasions over a two-year period – with both identifying identical breaches.
Nathan Cook, HSE senior enforcement lawyer, told Chester Magistrates Court how a visit in December 2019 found significant breaches of the Control of Substances Hazardous to Health Regulations 2002 (COSHH) – resulting in six improvement notices being served. These included requirements for the company to undertake statutory examinations of its wood dust extraction systems and to undertake face fit testing for those employees required to wear tight fitting face masks.
However, another visit to the same premises in November 2021 found identical breaches and again improvement notices were served. Pineland Furniture Limited pleaded guilty to breaching regulations 7(1) and 9(2)(a) of COSHH.
Asbestos
Several businesses have been prosecuted in the last 12 months for asbestos issues. In September 2022, Poundland Limited was fined £565,000 and ordered to pay £75,000 costs for a series of asbestos management failures. They hired asbestos consultants to survey their Ipswich building, which was found to contain asbestos in several locations. The consultants undertook annual monitoring visits, but Poundland did not prepare an asbestos management plan to ensure that the asbestos remained in a safe condition.
In October 2022, two directors of a construction company were fined after failing to ensure the safe removal of asbestos from a plot of land. They allowed the uncontrolled removal of asbestos and increased the risk of spread and exposure to asbestos panels by allowing it to be broken up with hammers before being bagged for disposal. Each was fined £1,400 and ordered to pay costs of £2,418.33.
In November 2022, Eddie Stobart was prosecuted for failing to carry out an asbestos survey during construction work. Several workers complained about the dust created when excavating and backfilling old buildings. An investigation by HSE found an asbestos survey had not been carried out prior to the work beginning to determine if any of the excavated material contained asbestos. There was no risk assessment and the workers involved hadn’t received any training in relation to asbestos. The company was fined £133,000 and ordered to pay costs of £9,260 by Manchester Magistrates Court.
In January 2023, the TUC called for new legislation requiring removal of all asbestos from public buildings, rather than the current policy of “managing” it.
Asbestos is still the biggest workplace killer according to the Health and Safety Executive, and Britain has the highest rates of mesothelioma cases in the world. But new research reveals that the majority of NHS buildings – including hospitals, health centres, blood donor clinics and GP surgeries – still contain asbestos more than 23 years since its use was banned in new buildings.
There is no safe threshold of exposure to asbestos fibres – inhalation even of small quantities can lead to mesothelioma, decades after exposure. The TUC says that where asbestos is still present, it is not safe to assume there will be no disturbances that put working people in danger. The only way we will eradicate asbestos cancer is with a legal duty to safely remove asbestos, and a clear timetable for its eradication.
In November 2023, RoSPA reported that each year around 400 women die from mesothelioma caused by asbestos in the UK, yet the majority were not directly exposed to the deadly fibres through their work. For men diagnosed with mesothelioma (an asbestos-related disease), in most cases an occupational link to asbestos exposure can be identified. For women, this is generally not the case.
A 2020 study involving mesothelioma patients (the GEMS study) suggested that the emphasis on the risk of exposure to asbestos in high-risk occupations, such as construction, may have obscured the risk of exposure in low-risk occupations, such as education, healthcare and administration. Women working in these areas were more likely to have been indirectly exposed to asbestos in potentially contaminated work environments than to have had direct exposure. This is particularly the case, the study says, where the buildings in which they worked (schools, hospitals, offices), were built at the height of asbestos use and are now beginning to age and decay.
Buildings that people use in their daily lives, such as workplaces, schools and hospitals, are the focus of a new HSE campaign to keep people safe from asbestos. The HSE wants anyone with responsibilities for buildings to do everything they must to comply with the law and prevent exposure to this dangerous substance, which was widely used in post-war construction before it was completely banned in 1999.
The HSE will check how asbestos is managed when visiting a range of buildings – such as schools and hospitals – requiring those responsible for managing asbestos risks to ensure they have the right arrangements in place.
Legionella
Back in August, Legionella hit the headlines when asylum seekers being housed on the Bibby Stockholm barge were all removed after traces of Legionella bacteria were found in the on-board water system. The Home Office said all 39 migrants on board the vessel in Dorset were disembarked as a precaution.
Legionella bacteria can cause Legionnaires’ disease - a type of pneumonia. People contract Legionnaires' disease by inhaling small droplets of water (aerosols), suspended in the air, containing the bacteria.
A Home Office source told the BBC that results showing "low levels" of Legionella in the water system on the Bibby Stockholm were received by a contractor.
During the pandemic, there were concerns that symptoms of Legionnaires' Disease, which include a cough, shortness of breath and high fever, were similar to those of COVID-19.
Stuart Gizzi, Managing Director at plumbing equipment manufacturer Intatec said:
“It’s upsetting to learn that people are getting ill from Legionella when it is so very easily preventable. The early symptoms are similar to COVID-19, so for anyone suffering from it, there’s an extra worry. It’s a serious disease that has a 10% fatality rate.”
Due to the fact that many buildings were left unoccupied during the pandemic, the HSE warned that water system stagnation could occur due to lack of use, increasing the risks of Legionnaires’ Disease. The HSE advised building owners to review their risk assessment and manage the Legionella risks when they:
- Reinstate a water system or start using it again; and/or
- Restart some types of air conditioning units.
Any water system, with the right environmental conditions, could be a source for Legionella bacteria growth. There is a reasonably foreseeable Legionella risk if your water system:
- Has a water temperature between 20-45°C.
- Creates and/or spreads breathable droplets, e.g. aerosol created by a cooling tower, or water outlets.
- Stores and/or re-circulates water.
- Likely to contain a source of nutrients for the organism to grow, e.g. rust, sludge, scale, organic matter and biofilms.
The most common sources of Legionella are in man-made water systems including:
- Cooling tower and evaporative condensers.
- Hot and cold-water systems.
- Spa pools.
Other hazards
A company in York that was employed to decontaminate a hospital where the first cases of COVID-19 in the UK were found was fined more than £16,000 after staff were left with life-changing medical conditions after being exposed to ionised hydrogen peroxide.
Workers at Bio Decontamination Limited attended Scarborough Hospital on 18 September 2019 after being hired to carry out decontamination of the Aspen ward. The company used ionised hydrogen peroxide to decontaminate the rooms in the ward. It failed to appropriately seal the rooms, meaning the ionised hydrogen peroxide escaped into the adjacent corridor where hospital staff were working.
Three members of hospital staff required treatment at the Accident and Emergency department after being exposed to the substance. They suffered from itchy skin and became lightheaded. All three continue to suffer with life-changing medical conditions as a result of their exposure and struggle to carry out day-to-day tasks or work.
An investigation by the HSE found that the work had not been properly risk assessed prior to being undertaken. The employees carrying out the work were not appropriately trained nor supervised and the working practices displayed were below the required standard. The level of ionised hydrogen peroxide was not adequately monitored to warn of release, exposing people to dangerous levels.
The Control of Substances Hazardous to Health Regulations (COSHH) require you to adequately control exposure to materials in the workplace that cause ill health. A COSHH assessment concentrates on the hazards and risks from hazardous substances in your workplace.
Health hazards are not limited to substances labelled as 'hazardous'. Some harmful substances can be produced by the process you use, for example:
- Wood dust from sanding.
- Silica dust from tile cutting.
- Fumes from welding.
Think about:
- How workers might be exposed (whether the substance can be breathed in, get onto or through the skin or can even be swallowed) and the effects of exposure by each of these routes.
- How often people work with the substance and for how long.
- Anyone else who could be exposed - do not forget maintenance workers, contractors and other visitors or members of the public who could be exposed.
- What you're already doing to control the risks.
- What further action you need to take to control the risks.
- Who needs to carry out the action.
- When the action is needed by.
Commenting on the responsibilities building and facilities managers in preventing exposure to hazards, Claire Deacon, Director of health and safety services at International Workplace, says:
“Commercial building owners and those who are responsible for facilities, including building maintenance, need to be reminded of the need to ensure suitable and sufficient property risk management. Inspections need to be carried out by a professional, who can give advice and put programmes in place to ensure conformance.
“Clearly not everyone who manages or owns buildings knows how to treat the problem. Competent structural engineers and professionals should be used to identify and determine the integrity and ongoing safety of a particular structure.
“All commercial building owners in the United Kingdom have duties under the Health and Safety at Work etc. Act 1974, which extends to a wide range of risks such as Legionella bacteria, asbestos, fire safety and many other hazards that may arise from the building fabric and its work activities. Thus, a proactive approach is always strongly advised to reduce risk. Actions should include regular inspections and maintenance. Failure to do so would be a failure to meet basic health and safety obligations. Not taking action could lead to a risk of prosecution for non-compliance with statutory legislation.”
International Workplace's Legionella Awareness training course ensures your organisation meets the Approved Code of Practice: Legionnaires' disease: The control of Legionella bacteria in water systems (L8). Learners will leave this course with a thorough understanding of their responsibilities and how to manage the risks associated with Legionnaires’ disease.
Our Asbestos Awareness training course has been designed to help you understand how to manage asbestos in the workplace and recognise the risks. The content of the course is stipulated in the L143 Approved Code of Practice for the Control of Asbestos Regulations (CAR) 2012.